2, rue de la Ternière
Avrille Cedex FRANCE
- 35 million sockets designed per year
- Co-designer of custom fasteners for 100 years and manufacturer of standard products
- From M6 to M10 and from 8 mm to 30 mm (internal diameter adapted to the passage of a screw)
- Steel, stainless steel, brass, etc. (other materials are available on request).
A socket designed for the precise centering and alignment of assembly components. Frequently used for centering two half-cases (transmission belt housing, bearing centering, gearbox housing, etc.).
Rectified socket - Centering socket - Positioning socket
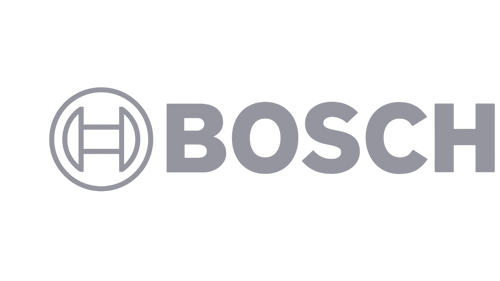
Rectified socket - Centering socket - Positioning socket
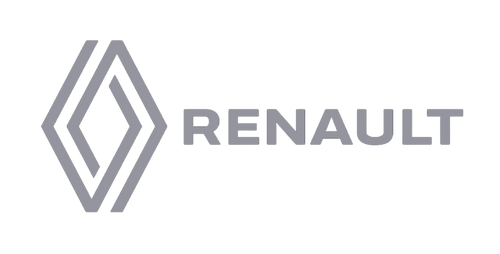
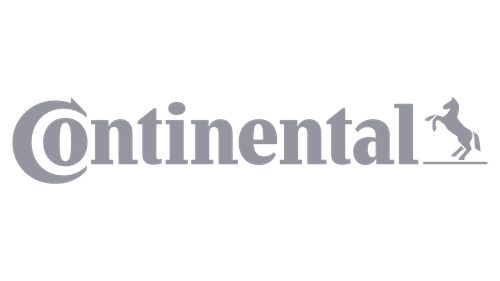
- Feasibility control using the FMEA tool, which is used to analyze failure modes, their effects and their criticality.
- Manufacture of initial samples in medium series, and validation of production with PPAP according to the IATF 16949 standard.
- Development of detailed production processes according to the APQP quality process
- Collection and analysis of production data to identify trends and variations. 3PPM in 2023.
The advantages of LGC Industries manufacturing
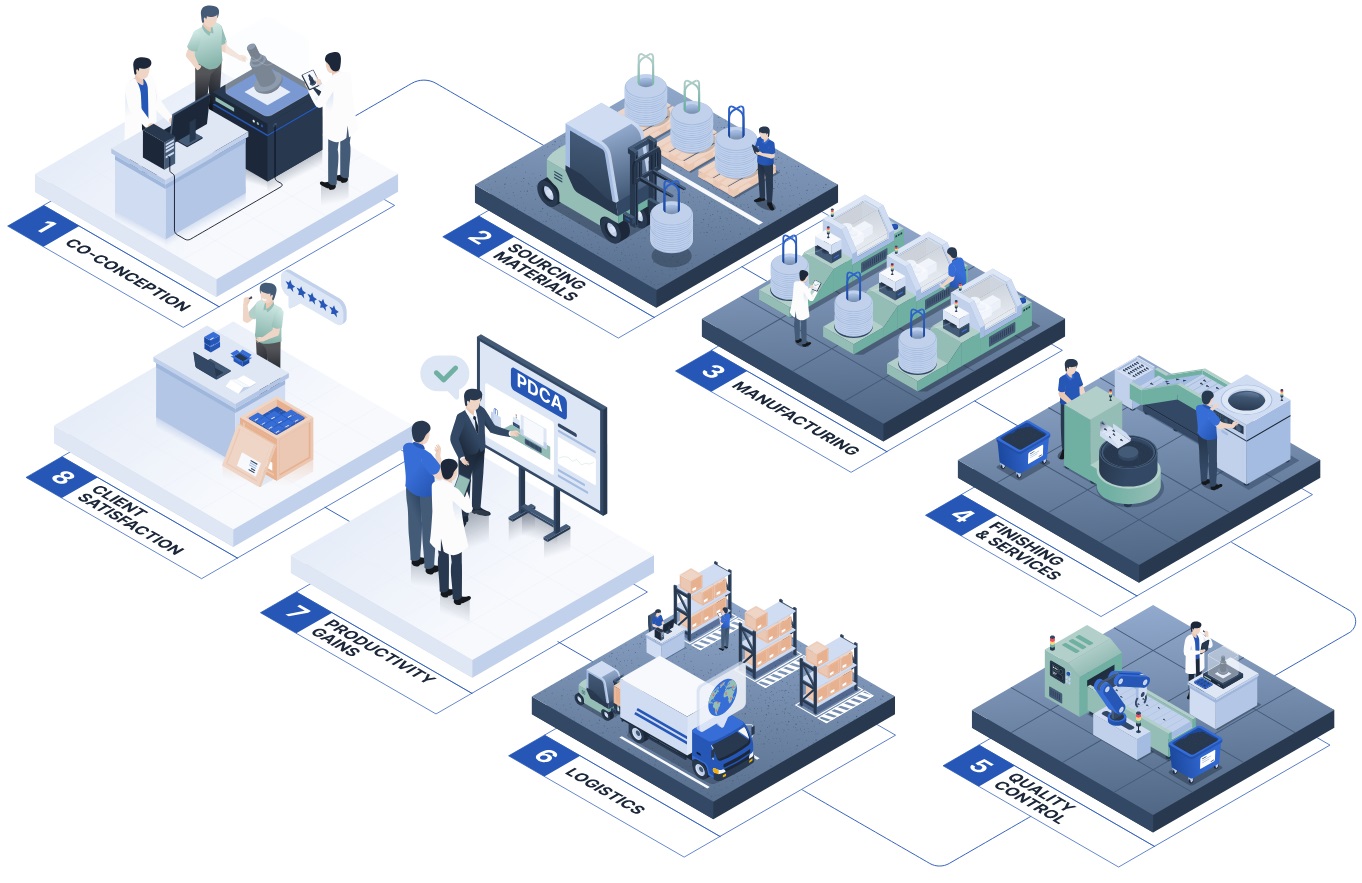
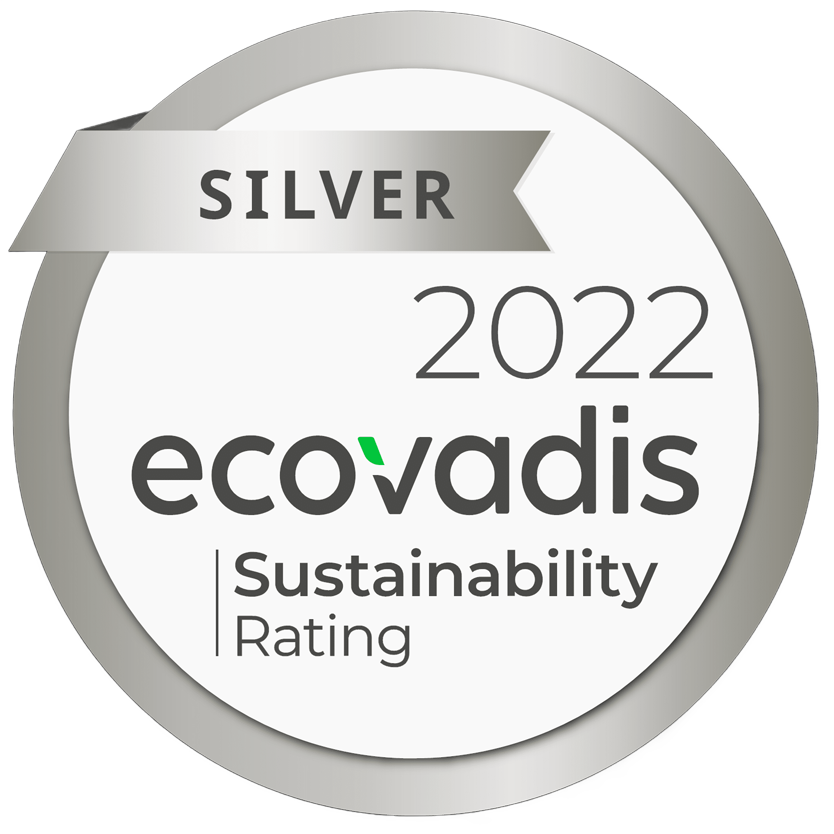
.png)

.png)


- 24 Multi-spindle lathes
- 45 Spins Escomatic
- 42 Fluting machines
- 8 Plunge and thread grinding machines
Learn more about the technical characteristics of our products
Discover other products
Optimize your assemblies with a rectified socket
The sockets rectified, which is commonly called”positioning socket or centering socket” play an essential role in mechanics and industrial assembly. They guarantee the precise positioning of the components, thus reducing the risk of deformation of the parts or of uncontrolled movement. These small positioning elements are often overlooked, which may explain in some cases the decline in the overall performance of a mechanism.
La rectified socket or centering socket turns out to be the jewel of the assembly. The rectified socket ensures perfect alignment of the parts, thus eliminating discrepancies and unwanted friction. Frequently used in complex mechanical systems, this small cylindrical part will become the keystone of the precision of your assemblies.
What is a rectified socket?
Les rectified centering sleeves are extremely precise cylindrical assembly elements designed specifically to ensure the precise centering and positioning of 2 components in an assembly.
Their innovative design prevents any risk of entanglement, which is essential for automated assemblies. Thanks to our specialized production resources, we guarantee a quality level close to zero defects, 0 PPM.
Unlike a pin or a centering pin, the ground socket can accommodate a through screw, thus offering greater flexibility in applications.
How are LGC ground sockets made?
There are two different methods for creating a socket
From pin to ground socket
It is possible to start from a solid material that has been machined in order to arrive at a shape of pin. In this specific case, it is necessary to drill a pin to make it hollow, this is called a bore, which complicates the process both financially and technically and environmentally.
From the tube to the rectified socket
In a second case, it is possible to make a positioning socket starting from a tube.
The use of a tube is highly recommended because it perfectly meets all criteria (precision, price, quality and also carbon footprint).
That's the technique we use at LGC.
The first step in making a socket is cutting the raw material.
The raw material is in the form of long, hollow tubes.
The material and the diameter depend on the desired final part.
The tube enters a machine which cuts it to the desired length.
The socket can be further machined with specialized machines.
For example, chamfers may be required or finishes on the material may be applied.
The socket then goes through a stage of rectification.
A roller presses the parts against a grinding wheel rotating at high speed.
It is the wheel that, by abrasion, will modify the diameter of the part to reach precise tolerances of a few microns (~5-6 μm).
What are the advantages of using a rectified socket?
- Dimensional accuracy: a rectified socket guarantees impeccable dimensional accuracy. By creating a uniform space between the components, the rectified socket eliminates potential errors associated with differences in dimensions or alignments between 2 parts.
- Structural stability: the rectified cylindrical socket, with its sturdy shape, provides exceptional structural stability. It is resistant to vibrations and mechanical loads, ensuring optimal performance under demanding conditions. This is why we find almost all the engines of our vehicles.
- Reduction of friction: thanks to its intelligent design and the grinding process, the ground bushing minimizes friction between moving parts. This results in reduced wear and extended component life.
Do you want to learn more about the steps in the manufacture of our sockets?
Go to our dedicated article: Everything you need to know about LGC sockets